Resources > Case Study > Radix IoT Helped A Coal Mine Gather Data from Their Existing Systems to Improve Safety
Radix IoT Helped A Coal Mine Gather Data from Their Existing Systems to Improve Safety
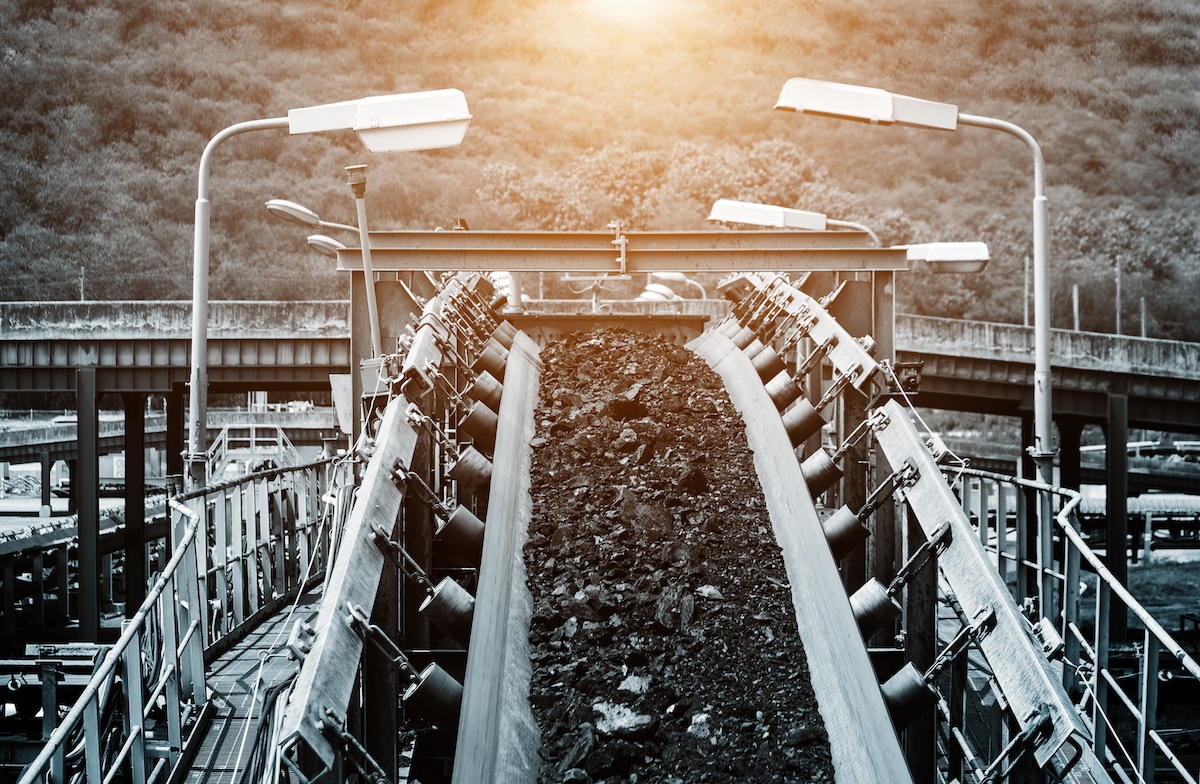
Overview
The client operates a large open cast coal mine, spread over a wide geographic area. Within this mine there are 25 overland conveyors – some as long as six kilometers. There is a control room that monitors and controls all of these conveyors, however, managers lacked the ability to report on maintenance carried out. There is some maintenance that must be completed - all conveyors and protection systems must be tested, by law, monthly. On a single conveyor belt there is a trip switch on either side every hundred meters. In many cases there are in excess of one hundred safety devices that need to be checked to ensure proper functionality.
Initially the client wanted to incorporate the maintenance reporting within their existing automation systems. However, it became clear that the cost to do so made this option difficult to justify. To further complicate matters, there was a mixture of existing systems that control the coal plant, all of which would have to interoperate with the maintenance reporting system.
Mango proved to be both affordable and compatible with the equipment the customer already had installed on site. Maintenance reporting was important as well, to not only comply with government regulations, but to be able to quickly create a report to prove it. Real-time alarming connected to the customer’s email system kept all responsible parties alert to time sensitive or emergency events, while historical data made reports from any designated time frame possible.
Approach
The Mango server is housed in the main control room at the coal plant one KM away from the mine. In Mango each conveyor ModBus TCP gateway was added as a ModBus IP data source. The polling was set at two seconds for each device. On each data source, six ModBus registers were added as data points to read key information from each microcontroller, for example: the status of the conveyor belt, which device was tripped, and was it a left or right trip? As some of the ModBus registers on the microcontroller were bit information, meta data points were created using JavaScript to provide statistical information like conveyor availability. Alarms within Mango were set up to alert by email whenever a data source exception was raised after a settimeout. Additionally, event detectors were created to set virtual data points to indicate communication failure on the DGlux HMI. All the created data points were set up in the point hierarchy to ensure a clear data structure within DGlux.
Results
Using Mango allowed the control center to see every device that was being tested. In addition the client can create reports using the data within any chosen time frame. This helped the client to not only operate within the confines of the law, but also from a commercial perspective in that the maintenance supplier was monitored. They saw first-hand that the implementation of Mango was simple, easy and cost effective, especially given the timeframe and scope of the project. Hardware and software choices were easy to make because Mango is compatible with numerous platforms.
At Radix IoT, we’re all about empowering our customers with the visibility and data insights needed to more effectively manage their operations. Our Mango IoT platform–leveraged by telecom, energy, datacenters and facilities’ operations worldwide– seamlessly connects and unifies data from pre-existing assets and systems, enabling our customers to more proactively manage their operations and better protect their bottom line. We invite you to learn more – request a demo today!